一、为什么要做FMEA?
1、一张图告诉我们为什么要做FMEA
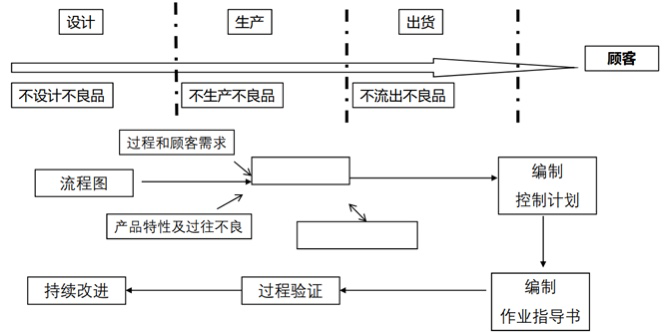
FMEA贯穿整个新产品开发的过程,设计阶段的潜在失效分析分析我们叫DFMEA设计失效模式与影响分析(Design Failure Mode and Effects Analysis)。过程开发阶段的过程潜在失效模式及影响分析叫PFMEA(Process Failure and Effects Analysis)。FMEA在整个新产品开发过程中起着至关重要的作用!
2、FMEA分析流程步骤
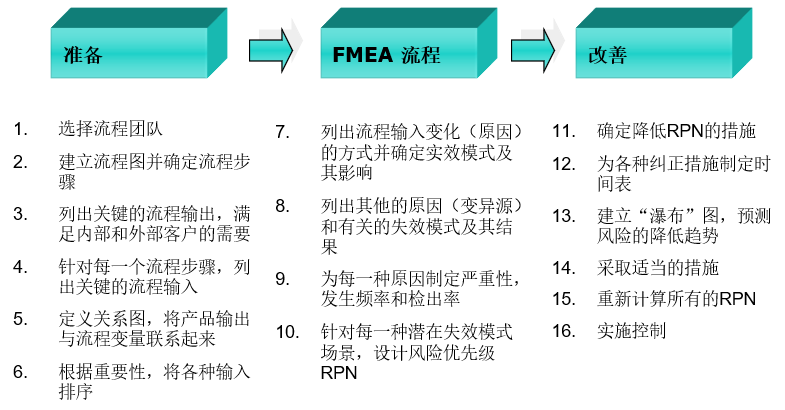
3、FMEA的应用
1)对于新产品过程开发,其进度时间在可行性分析/过程流程图确定之时,在生产工装备之前/PPAP批准之前;
2)须考虑从单个部件到总成的所有的工序/工作站:包括在厂房里能影响生产和装配运作的所有过程,例如装运,接收、材料运输,存储,运送或标签。
4、FMEA的要求与说明
4.1 PFMEA的主要作用
1)确定过程功能和要求;
2)确定与产品和过程相关的潜在失效模式;
3)评价失效模式对顾客产生的后果影响;
4)确定相应的关键特性和重要特性,并明确标示;
5)确定制造过程潜在起因及要采用控制措施来降低失效频度或失效探测度的过程变量,以此聚焦于过程控制;
6)编织一个潜在失效模式分级表,以便建立一个考虑预防/纠正措施的优选体系。
7)记录制造或装配过程的变化点和结果,文件化制造或装配过程控制内容和要求。
4.2 PFMEA的主要目的
1)是在新车型或零件项目的制造策划阶段,对新过程或修改的过程进行早期评审和分析,以便促进预测、解决或监控潜在过程问题,减少制造风险;
2)PFMEA 有助于对制造过程中问题的早期发现,从而避免和减少晚期失效带来的损失,PFMEA 的结果能为制订质量控制计划和过程控制提供正确的、恰当的根据;
3)PFMEA能引导资源去解决需要优先解决的问题。
4.3 创造性
PFMEA是一个创造性的工作,需要采用跨功能的小组。
小组中有位FMEA经验的协调人是很有帮助的,除非责任工程师有FMEA和小组协调检验。
协调员负责每次做FMEA分析的整个过程。开会前准备,开会时如何组织,保证有效输出,及前后的跟进。对协调员要求比较高,既要有专业的FMEA工具知识,且对过程/产品熟悉,还要有组织沟通统筹能力!
4.4 PFMEA建立/更新的时机
1)新的/更改的零部件;
2)在各个开发阶段中,当产品/过程设计有变化或得到其它信息时;
3)改进产品/过程设计时;
4)DFMEA要及时反映最新的产品更改级别和最新的相关实施措施。
4.5 第四版的过程PFMEA
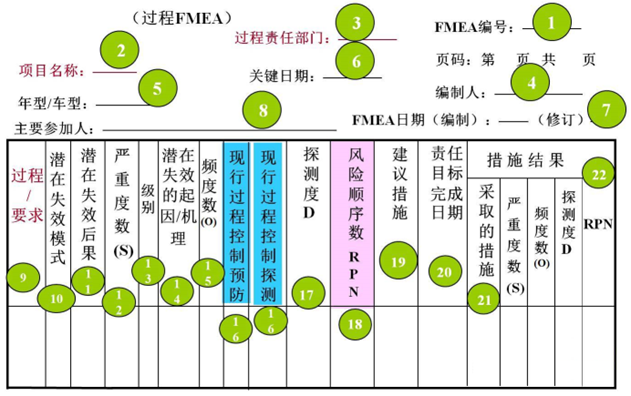
4.6 PFMEA建立详解
1)FMEA编号:填入FMEA文件编号。
2)项目名称:填入项目的名称或系统,子系统,零件的名称及编号。
3)过程责任部门:填入整车厂,部门和小组.如适用,包括供应商的名称。
4)编制人:填入负责编制FMEA的工程师的名字。
5)年型/车型:填入所分析的设计将要应用和/或影响的年型/车型。
6)关键日期:填入初次FMEA应完成的时间。
7)FMEA日期(编制)/(修订):最初完成的日期/修订日期。
8)主要参加人/核心小组:负责设计开发FMEA的小组成员。
4.7 FMEA的顺序概述(9-22)
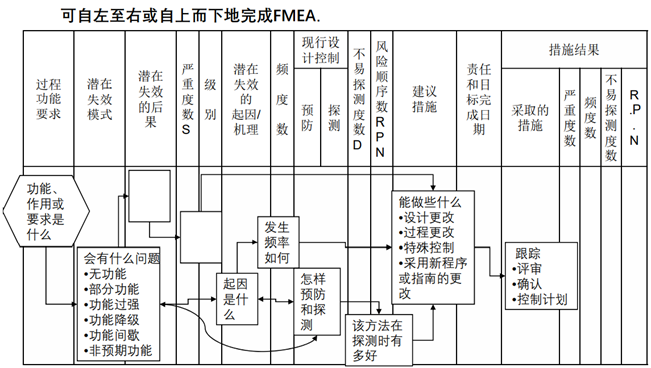
二、PFMEA建立
1、PFMEA建立详解
1)FMEA编号:填入FMEA文件编号。
2)项目名称:填入项目的名称或系统,子系统,零件的名称及编号。
3)过程责任部门::填入整车厂,部门和小组.如适用,包括供应商的名称。
4)编制人:填入负责编制FMEA的工程师的名字。
5)年型/车型:填入所分析的设计将要应用和/或影响的年型/车型。
6)关键日期:填入初次FMEA应完成的时间。
7)FMEA日期(编制)/(修订):最初完成的日期/修订日期。
8)主要参加人/核心小组:负责设计开发FMEA的小组成员。
2、FMEA的顺序概述
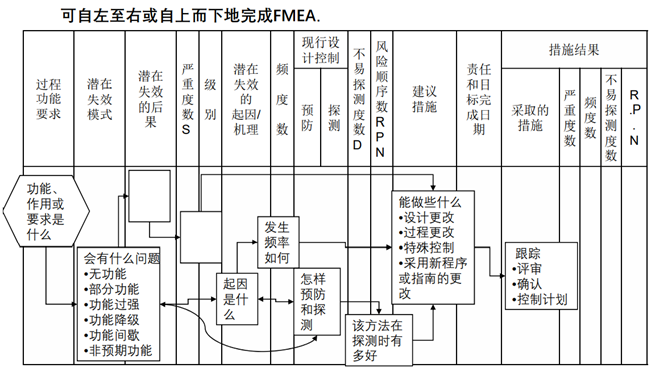
2.1 过程功能/要求
1)简单描述被分析的过程或工序(如车/钻/功丝/焊 接/装配)。
2)尽可能简单说明该过程/工序的目的,列出相应的过程/工序编号。
3)若包含许多具有不同失效模式的操作,可将操作列为独立的过程。
4)小组应评审适用的性能、材料、过程、环境和安全标准。
5)可增加一列:过程工序中涉及的产品特性编号。
6)有助于系统地分析所有特性的失效模式。
备注:在“过程功能”和“描述”栏所需添入的内容与工艺流程文件相同。
7)识别该工序目的、要求/产品功能、特点
目的:
1)必需弄清产品的设计意图或过程目的/要求(总成/零件/工序图/SPEC等)
2)以帮助决定每个功能特性或功能项目的潜在失效模式
2.2 失效模式
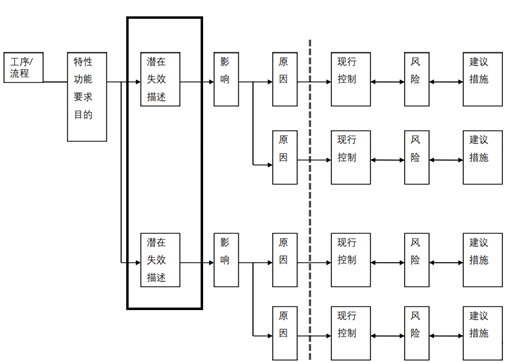
1)所谓潜在失效模式是指过程可能发生的不能满足过程或设计要求的状况。是对某一作业可能发生的不符合性的描述。
2)建立P-FMEA时,要假定设计的产品会满足设计要求。不依靠改变产品设计来克服过程中的重要环节,因设计缺陷产生的失效模式一般不需包含。如要包含,则它们的影响及避免措施由D-FMEA来解决。
3)跨功能小组应讨论先前作业的失效模式,并假定先前的失效模式不带入本作业。
4)失效状态是以作业为单元进行。只有以作业为审查单元时,才能把失效模式与产品和过程要求/特性相联系。上游作业中的失效模式应在那层进行表述。
注意:
1)实现项目功能及过程要求可能出现的问题:冲压裂纹,附着性差,不耐腐蚀,缩松…
2)建立新产品的失效模式清单,是一种创造性和预防性的工作,分析、评价各种可能发生的情况。
3)对现存产品而言,可从产品或作业的质量记录中列出符合实际的失效模式清单。可从标准表格中选出失效模式,以强调统一性。
4)检查工序不要过多考虑进行FMEA分析。
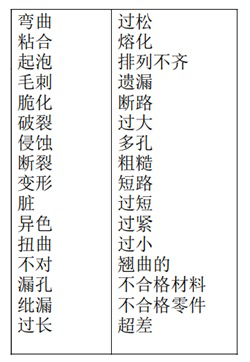
2.3 后果影响、严重度和级别
失效模式的后果影响
1)后果影响是指失效模式对顾客的影响。
2)顾客泛指下步作业、后续工序、装配厂、服务运行、最终用户和政府法规。
3)当顾客是后续作业时,这种影响应描述为过程的具体表现。(如:粘着于模具、损坏夹具、装配不上,危害操作者等等)
4)当顾客是最终用户时,这种影响应描述为产品的具体表现。(如:外观不良、噪音太大、系统不工作等)。
5)若失效模式可能影响安全或导致违反法规(特殊特性),需清楚描述。
部分通常的后果影响清单
□外观不良 □功力损失
□顾客不满意 □时强时弱
□影响美观 □不能上锁
□不能紧固 □不可显示
□异色 □配合性差
□工件在后续作业中阻塞 □粘着于模具
□雨水进入汽车 □等等
注意:
1)确定这种影响需要了解产品, 以及设计工程师的参与
2)同类产品/零件DFMEA和 PFMEA文件是有用的参考资料
失效模式的后果影响举例
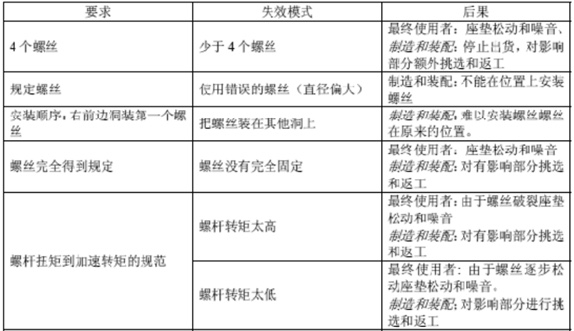
文章来源于网络,版权归原作者,侵删。