一、什么是FMEA
FMEA(Failure Mode and ffect Analysis)即失效模式及效应分析,是一种用来确定潜在失效模式及其原因的分析方法。它是在产品设计阶段和过程设计阶段,对构成产品的子系统、零件,对构成过程的各个工序逐一进行分析,找出所有潜在的失效模式,并分析其可能的后果,从而预先采取必要的措施,以提高产品的质量和可靠性的一种系统化的活动。具体来说,通过实行FMEA,可在产品设计或生产工艺真正实现之前发现产品的弱点,可在原型样机阶段或在大批量生产之前确定产品缺陷。FMEA实际上意味着是事件发生之前的行为,并非事后补救。
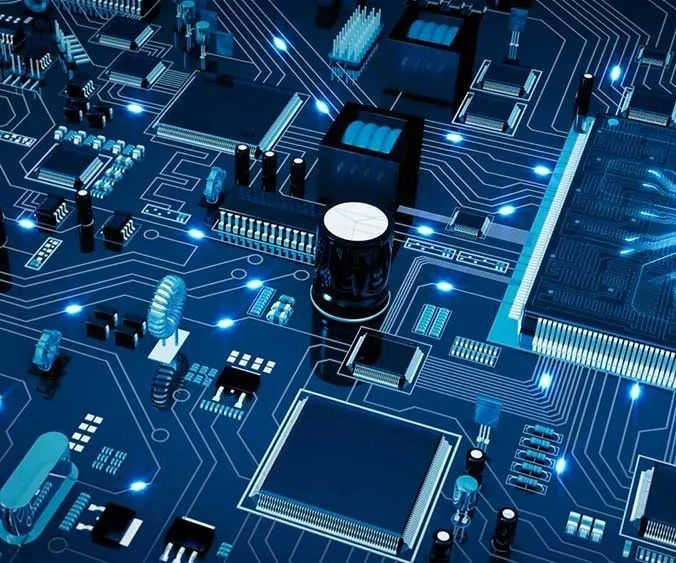
1、减少制造过程中的废品和停工时间,提高生产效率。
2、降低制造成本,提高产品质量。
3、提高设备可靠性和安全性,减少事故发生。
4、提高员工安全意识,减少工伤事故。
5、加快产品上市时间,提高企业竞争力。
6、为产品设计和改进提供基础数据,减少重复劳动。
7、通过分析失效原因,提高对新产品的预防性设计。
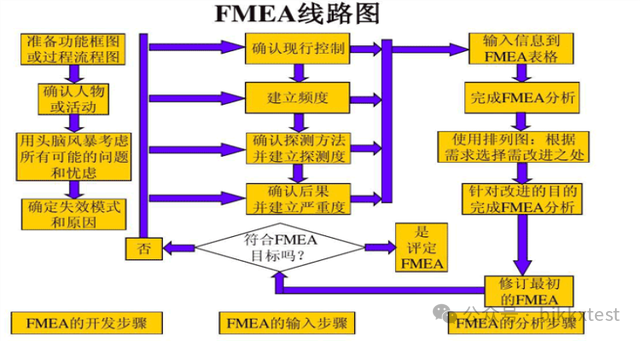
三、失效和失效模式
对于产品质量的理解,即想办法让用户(消费者,使用者,维修者)在产品使用过程中,没有造成任何正常功能的影响。对于管理的理解,即寻找方法,利用资源,达成质量目标。而FMEA 作为质量管理的工具,可以从全局的角度做好风险分析,风险和成本之间寻找平衡,最好确定控制手段。
FMEA比较重要的一点是要站在用户的角度看问题,分析技术风险,设计和生产流程风险,减少失效,提高产品安全性。首先是理解失效,即没有达到既定的功能和要求。
🔺功能丧失:无法操作,突然失效;
🔺功能退化:性能随时间损失;
🔺功能间歇:操作随机开始、停止;
🔺失效模式:是指看到或者感知到现象;
🔺失效影响:是指用户的切身感受。
四、FMEA分析步骤
1、定义范围:项目识别 项目计划、分析边界、经验教训等;
2、结构分析:系统结构 可视化分析范围、识别设计接口、交互或过程等;对于结构分析,同为FMEA分析的DFMEA和PFMEA,由于分析对象不同,进行结构分析的目的也是有所异同的。DFMEA的结构分析是为了将设计识别和分解成系统、子系统、组件和零件,以便进行技术风险分析。
3、功能分析:功能概述 可视化功能关系 识别功能、要求及产品特性;整个FMEA的核心步骤就是拆解功能,其目的,就是要确保相应的功能分配到合适的分解项中。某一个分解项的功能,描述的是这个分解项的预期用途。在DFEMA中,系统要素的功能是描述这个要素的预期用途。而在PFEMA中,描述的是过程项或过程步骤的预期用途。
4、失效分析:失效链 可视化失效关系 创建失效结构 识别变化来源。发生了什么失效影响?失效模式是什么?为什么会失效?(失效起因)。
5、风险分析:分配现有预防措施 预防/探测控制的分配 SOD评估 关联客户供方行动优先级等;风险分析的目的是通过对严重度、频度和探测度评级进行风险评估,并对需要采取的措施进行优先排序。
a.严重度评级S:是失效影响的严重程度,对于产品而言是失效发生的后果。FMEA手册根据失效影响的大小,将严重度分成10级,一般要看产品的安全性和有效性是否被影响到。而在PFMEA分析中,失效分析的对象是过程,过程的失效可能会影响到下一个工序,下一层级的产品加工,最终影响到产品的功能。
b.频度评级O:是失效起因发生的频率,对于产品而言是失效发生的概率。频度的大小,跟是否存在预防控制和探测控制有关。采取的控制措施越多,那相应发生失效的频度就会越低。预防控制提供信息或指导,是设计的输入。DFMEA可能包括:法规和标准的要求、使用材料的标准、文件的要求、以往的经验等等,对于硬件设计还可能是规范的流程、设计评审机制,checklist等等。PFMEA可能包括:SOP、设备维护、人员培训等等。
c.探测度评级D:是失效起因和/或失效模式的可探测的程度,在于是否有有效和可靠的测试或检验方法探测到失效模式或失效起因。在进行探测度评级时,最主要是要看探测的方式是否成熟和探测的机会。比如:测试或检验的方法都是通过了验证的,那肯定比还没有建立检测方法要更具探测能力。
d.措施优先级AP:措施优先级就是在采取降低风险之前,由于资源、时间、技术和其他客观因素的限制,决定采取措施的优先顺序。判断优先级主要是通过S*O*D得到的数值大小,但是新版手册对此有了新的规定,首先考虑的是严重度,其次是频度,最后才是探测度,这与之前只比较数值的大小不同,避免出现相同数值的乘积而影响到优先级排序。
6、优化:采取措施降低风险 明确职责和期限实施并记录行动确认实施的效果 持续改进。先要明确优化的目的,即在风险分析的基础上,确定降低风险的措施并且评估这些措施的有效性。降低风险就是要降低风险的严重度、降低风险发生的频度或者是提高风险可探测度。根据采取措施优先级的原理,优化的顺序也是先要消除或减轻严重度,其次降低频度,最后是提高探测度。
7、结果文件化:最终FMEA分析可以形成一系列的报告。最终FMEA分析可以形成一系列的报告,可作为设计开发的输入存在于设计开发文档中,用于指导新的设计或者经验借鉴。
五、FMEA是如何计算的
什么是风险优先数(RPN),以及它如何在FMEA中使用?
风险优先数(RPN)是一个数字,它被赋予流程过程中特定的步骤,以量化故障模式发生的可能性、故障没被检出的可能性,以及故障对人或设备造成伤害的严重性。
RPN是这三个因素的乘积:
1、故障发生的可能性;
2、故障不被检出的可能性;
3、故障对人或设备造成伤害或损害的严重程度。
在FMEA中,每个故障模式都会被分配导一个RPN,FMEA的目标是尽可能降低RPN,如果某个故障可能导致的影响非常严重,那么在产品发布或重新发布前,FMEA过程就会更加努力地通过纠正措施来降低风险。
它还可以通过一个简单的计算公式来得出,即是故障的严重乘以发生次数。
六、FMEA常见类型有哪些
1.系统FMEA(有时也称为概念FMEA)
在早期概念和设计阶段用于分析系统和子系统。系统FMEA主要针对由于系统缺陷而引起系统功能间的潜在故障模式。系统FMEA需要考虑系统与系统以及系统内部组成之间的交互作用。
2.设计FMEA
在生产阶段之前对产品进行分析。设计FMEA关注的是由于设计缺陷产生的故障模式。(注意:设备FMEA,针对环境因素和特性的FMEA是设计FMEA的一部分)。
3.过程FMEA
在生产和组装的过程中进行分析。过程FMEA关注的是由于生产或者组装缺陷而产生的故障模式。
4.服务FMEA
在产品到达用户之前对服务进行分析。服务FMEA关注的是由于系统或过程缺陷而产生的故障模式(任务、错误、缺陷)。
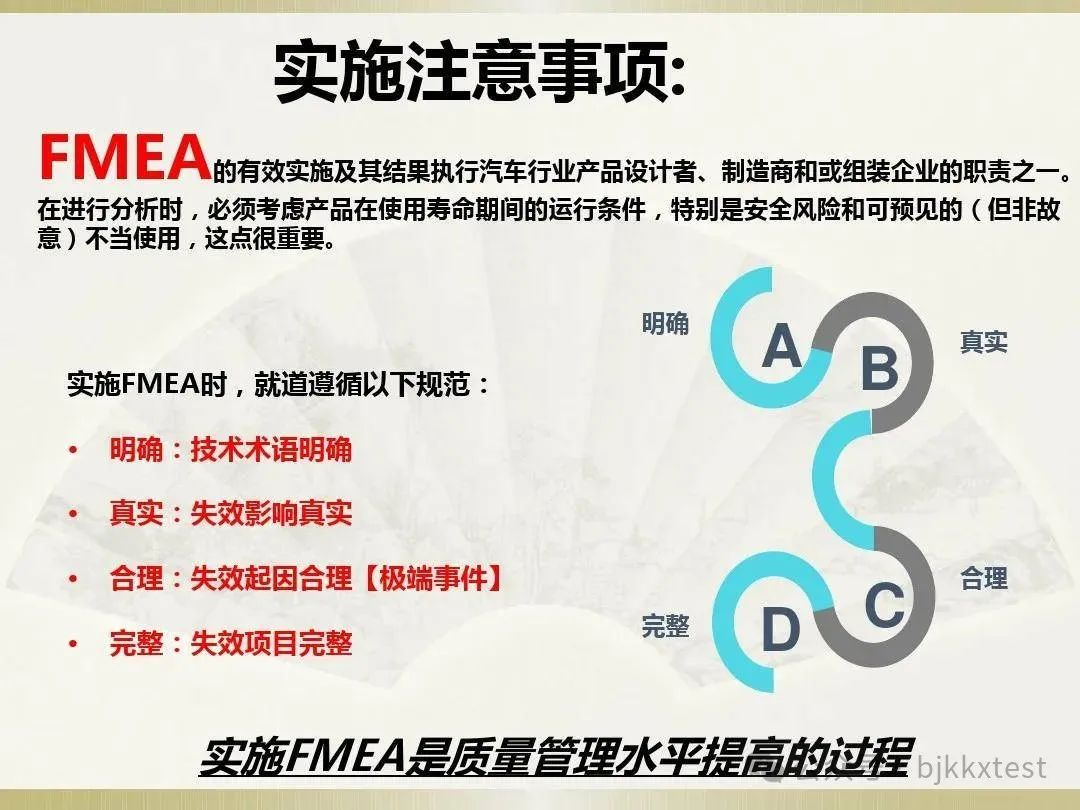
不管是产品的功能设计还是产品的使用风险分析,首先是要做的就是站在用户的角度去看问题,站在用户的角度看需要哪些功能,可能存在哪些技术风险,以提高可靠性。缺陷的预防比缺陷的结果更有意义,拿硬件设计来讲,前期没有做好充足的设计检查和风险检查,出现问题后改板往往会花费更多的时间精力。
文章来源于网络,版权归原作者所有,侵删